Top 10 Must-Know Boeing 787 Engine Q & A
The Boeing 787’s engines are modern marvels—quiet, powerful, and just a bit too smart for their own good 🧠✈️. But let’s be honest: unless you’re best friends with N1, N2, and N3, trying to understand the engine systems can feel like decoding a foreign language full of valves, acronyms, and surprise EICAS messages ⚙️🔍. Don’t worry—we’ve got you covered! This Q&A breaks down the key concepts in plain language—with a few laughs along the way 😂. Whether you’re sim prepping, geeking out, or just tired of nodding and pretending you know what the EEC actually does, this guide is for you 🛫📘.
1. What engines power the Boeing 787, and what’s their thrust rating?
🛠️ The Boeing 787 can be powered by two different engine types, depending on the airline’s configuration:
- Rolls‑Royce Trent 1000 (commonly the D, TEN variants)
- General Electric GEnx‑1B
Both engines are high-bypass turbofans designed for long-haul efficiency, fuel savings, and low noise.
- The Trent 1000 delivers up to 76,000 lb of thrust, with most models rated around 70,000–74,000 lb.
- The GEnx‑1B offers a similar thrust range, up to 76,100 lb, depending on the variant.
Although they differ in internal architecture and engine logic, both are fully interchangeable from a certification standpoint—though not physically interchangeable on the same aircraft. Operators choose based on performance goals, maintenance programs, and existing fleet commonality.
2. Explain the three-shaft core architecture: N1, N2, and N3.
- N1: Fan and low-pressure (LP) turbine on a common shaft.
- N2: Intermediate-pressure (IP) rotor, connected to the accessory gearbox.
- N3: High-pressure (HP) compressor and turbine on their own shaft.
This design enhances spool independence, performance, and response.
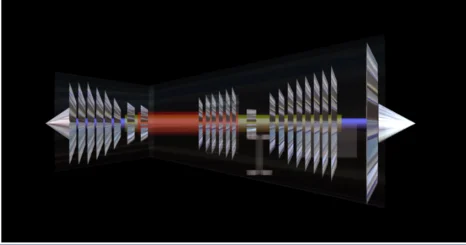
3. How does the 787 engine deliver fuel from tanks to the engine?
- Spar Fuel Valve in the main tank opens.
- First-stage pump adds pressure.
- Fuel passes first-stage filter.
- Second-stage pump significantly boosts pressure.
- Fuel Metering Unit (FMU), controlled by the EEC, regulates flow.
- Goes through second-stage filter, then
- Engine Fuel Valve, with flow monitored downstream.
4. What’s the purpose of the Fuel/Oil Heat Exchanger?
It serves dual roles:
- Pre-heats fuel (preventing icing).
- Cools engine oil while warming the fuel.
There’s also an Air/Oil heat exchanger that activates when fuel flow is low or fuel is already warm.
5. How is engine oil pressurized and circulated?
- Driven by N2 via the accessory gearbox.
- Oil flows through a filter, fuel/oil heat exchanger,
- Lubricates bearings, gearbox, accessory drives.
- Scavenge pump returns oil to tank; temperature and pressure are monitored.
6. Describe the ignition system and start sequence on the ground.
- Two ignitors per engine, managed by EEC.
- Ground start uses one ignitor; in‑flight auto‑start uses both.
- Starts use DC power chiefly, with standby backup.
- The APU is primary for start; external power (FWD/AFT) can supplement.
7. When and how is thrust reverse available?
- Active only on the ground, hydraulically driven.
- Cascade vanes reverse bypass airflow.
- Thrust levers must be at idle and moved into interlock.
- Autothrottle disengages, speed brakes deploy automatically.
- EICAS warns of ground/air logic faults like ENG REV LIMITED or ENG REV AIR/GND.
8. What are the primary engine indications displayed on EICAS?
Key indications:
- TPR, N1, EGT are primary.
- EGT has amber in continuous and red at takeoff/go‑around limits.
- Red alerts remain until acknowledged; redline exceedances persist.
9. What is the automatic engine start and relight logic?
- AutoStart uses starter‑generators to drive N2.
- If APU fails, external power supports start.
- AutoStart aborts on faults: hung start, hot start, no rotation, etc.
- In‑flight, auto‑relight tries restart after flameout, detecting low EGT/N1 or stall conditions.
10. Explain the Electronic Engine Control (EEC) modes and transitions.
- In NORM, engine thrust is based on TPR per thrust lever input.
- If sensors fail, alternate mode kicks in using N1:
- Soft alternate: automatic, keeps autothrust active.
- Hard alternate: manual mode shows commanded/target values.
- EICAS advises when EEC mode changes using ENG EEC MODE alerts